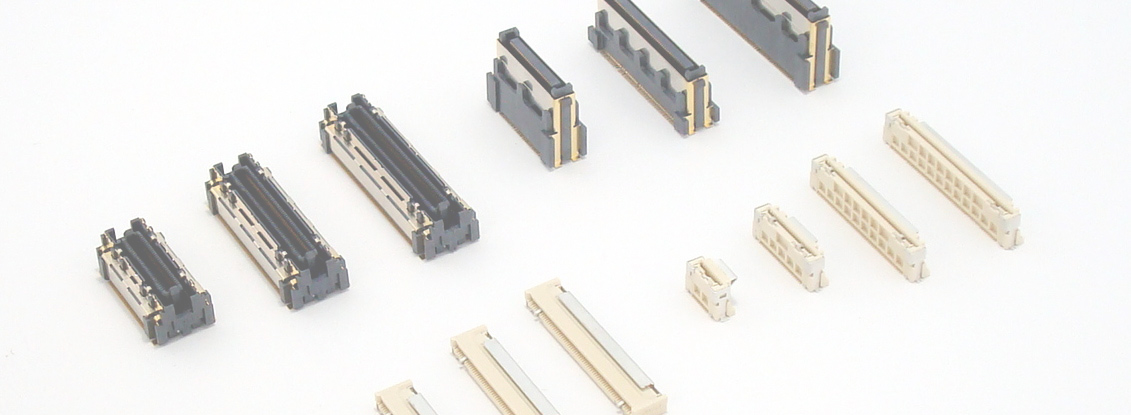
電気接続に関して「金属同士が触っていれば導通するんでしょ?」というのが、一般的な感覚なのではないかと思います。筆者もコネクタ業界に入る前、学生時代電気工学を専攻し、別業界で末席ですが技術者という肩書をもっているときですら、そういう感覚をもっていました。「なんとなくつないでおけば、つながるでしょ」というような感覚です。一方で、実験や評価において、接触不全、いわゆる「セットアップ」に不備があってうまくいかないなんてことも経験していました。そういうときは「仕方ないなぁ・・・」と、接続箇所を1つずつ点検して、ぎゅっと押し付けたり、ぽろっと外れたりしている所を直したりしました。でも工業製品がそれでは困りますよね?
「金属同士が触っていれば導通する」というのは、実は全く間違いではないのですが、この触るは、「しっかり正しく触る」である必要があります。加えて「余計なところに触らない」、「その状態を維持する」ことも必要になります。しかしながら、コネクタが使用される環境ではこれらを阻害するものがたくさんあるのです。今回は、接続不良の要因と対策について説明していきます。
コネクタの敵、その機能を完遂するために戦うべき相手は本当に多岐にわたります。その中の主なものを追っていくだけでも大変なので、最初に大きく分類してまとめていきます。
さて、コネクタの役割は「電気をつなぐべきところでつなぎ、つながらざるべきところをしっかり隔離すること」と表現することができます。よって、コネクタにおける接続不良は、大分すると次の2つの現象になります。
・ 非導通(オープン・開放) = つなぐべきところでつなげない
・ ショート・短絡および誤結線 = つながらざるべきところをつないでしまう
より細かく性能面まで目を向ければ、他にも高速信号の劣化等もありますが、ここではシンプルにこの2つに関して追っていきましょう。
すべての機能製品は最初から機能しない接続不良と、劣化によって故障してしまう接続不良がありますね。そのため、コネクタにおける接続不良の発生タイミングは、次の2つに分かれます。
・ 嵌合時からその直後(最初から機能しない・立ち上がらない)
・ 継続使用において(使っているうちに接続不良が出る)
次に接続不良を引き起こす要因ですが、人為的ミスによるもの、環境依存によるものの2つが挙げられます。さらに、2つめの環境依存によるものは、以下の3つに分けられます。
1.人為的ミスによる接続不良
(1)不完全嵌合
(2)誤嵌合
2.環境依存による接続不良
(1)機械的な影響による接続不良
(2)化学変化による接続不良
(3)異物による接続不良
コネクタの接続不良と発生タイミング、その要因をまとめたものが次の表です。
細かく見ていけば他にもありますし、見方によって分類が変わる場合もあるかと思いますが、大まかなところではこのように分類できます。それでは、分類毎にどのような対策がとられているのか見ていきましょう。
人はミスを含むさまざまな過ちを犯します。それはどんな人でも、犯しますね。もちろん些細なルールも破らない真面目な人やミスの少ない注意深い方もいれば、効率のためにはちょっとしたルール違反なら犯してしまう人もおっちょこちょいで同じミスを繰り返してしまう人もいるでしょう。いろんな人がいる前提で物事をうまく進めていくためには、それなりの対策が必要です。
たとえばルールが守られない場合やうっかりミスが起こったときに、そのルール違反やミスを犯す人のみが悪いのではなく、「守られないようなルール」「ミスを犯してしまうようなシステム」そのものが悪いという考え方があります。そういった場合、システムやルールの改善としてとられる手法は、下記のいずれかが多いのではないでしょうか。
① ルールや手順以外の作業をできなくする
② 正しい状態であること、もしくは間違いが起こっていることをその場で喚起し、知覚させる
③ 間違えそのものをあり得ないものにする(間違えても大丈夫にする)
製造現場では、作業者の安全や製品の品質を確保するためにさまざまな対策がとられます。たとえば、設備の可動部に手を入れないようにするために、離れた場所にある2つのボタンを両手で押さないと機械が稼働しない仕組みであったり、ポカよけと呼ばれる作業や仕掛品の接続不良を作業者に知覚させる仕組みであったりです。コネクタも、同じように対策がとられています。
さきほど、人為的ミスによる接続不良として不完全嵌合と誤嵌合の2つを挙げました。それぞれについて説明していきます。
不完全嵌合は、所定位置までコネクタを差し込まずに浅い位置で終わらせてしまったために、コネクタの中の端子同士が接触しなかったり、不安定にしか接触していなかったりする状態を指します。
対策として、次の2つが挙げられます。
これを防ぐ方法としてよく使われる手法は、完全に嵌合させてときにクリック感を出すという方法です。完全に嵌合したときに樹脂同士がパチンッと叩くようになる構造にし、クリック感を出します。加えて、このときに発生する音でも作業者に嵌合が完了したことを知覚させます。
これはシステムやルールの改善としてとられる手法②「正しい状態であること、もしくは間違いが起こっていることをその場で喚起し知覚させる」にあたりますね。当社製品では、FPC/FFCコネクタとして自動組み立てに対雄したロボット組立適合コネクタでもあるAuto I-Lockシリーズが、自動ロックがかかる瞬間にクリック感を発生させます。組立自動化対応にした製品ですが、手作業による組立を行っているいくつかのお客様からも「作業ミスによる不完全嵌合接続不良が解消した!」とお喜びの声を頂いております。
作業者の触感による知覚のみではなく、このクリック時のパチンッ、あるいはカチッという音が重要視されるケースもあり、Audible Click(可聴クリック)と規定されています。特に自動車のハーネスの配策作業等で、作業周辺の雑音環境に対してクリックで生じる音圧差は、dB(デシベル)値にて規定されています。そういったハーネス用のコネクタではAudible Click試験と呼ばれる試験があり、嵌合時に発生する音の強さの規定、検証を行います。
別の手法として、CPA(Connector Position Assurance)という機構もあります。言葉のとおり、「コネクタの位置を担保する」ための機構、すなわち「ちゃんと嵌合している」いうことを明確にする機構です。最近では電気的に検知する方法も実用化されており、「ちゃんと嵌合していないとかからないロック機構」というのが代表的なものです。たとえば、嵌合することでストッパー等が下がり、レバーを押し込めるようになるロック機構(図3)や、上から蓋のようにかぶせるロック機構等です。
ハーネス用のコネクタ、WtoBコネクタに適用されることが多い機構です。当社では現行品のラインアップでは準備しておりませんが、現在適用した製品の開発検討を行っています。
誤嵌合は、大きく分けると2つのケースが想定されます。
・ 作業環境で複数のコネクタが並んでおり、違うものにさしてしまう
・ コネクタの向きを間違った状態でさしてしまう
対策として、次の3つが挙げられます。
1点目のケースが特に起こりやすいは、車の配策や通信機の結線等ワイヤーハーネスを多数配策する場合です。同じコネクタを複数使うことが多々あるため、誤嵌合が起こりやすくなります。配策される側の工夫として、行先ラベルを付けたり、またそれをバーコード読み取りでチェックしたり等も実施されていますが、コネクタとして一番多くとられる手法は外から見えるプラスチック部分にカラーバリエーションを付ける手法です。
これによって作業者はどこにどのコネクタを挿したらよいかわかりやすくなりますし、後からミスも発見しやすくなります。こちらもシステムやルールの改善としてとられる手法②「正しい状態であること、もしくは間違いが起こっていることをその場で喚起し知覚させる」にあたりますね。
しかしこれではまだ、知覚されるだけで間違った場所への嵌合は可能です。そこでKey(鍵)と呼ばれる機構を付ける場合があります。よくある構造は、そのコネクタの基本構造に加えて組み合わせる雌雄のコネクタにそれぞれ溝と凸部をマッチングするように加えて、なおかつそれを位置違いで 何種類か準備する方法です。
こうすることで、間違ったコネクタに挿そうとしたとき、Keyが干渉して嵌合できないようにすることができます。
またこの有効性を検証するため、ある程度の力で無理に挿しても違う極性同士では嵌合せず、破壊もしないことを確認する試験としての用途もあります。これはシステムやルールの改善としてとられる手法①「ルールや手順以外の作業をできなくする」にあたるアプローチです。当社のWtoB製品である13065S+13065Bでも3種のキーコードを、13103S+13103Bでは2種のキーコードを準備しています。
もう1つの誤嵌合は、コネクタの向きを間違った状態で挿してしまうというミスです。このミスはほとんどの場合、挿すときの抵抗を無視している、あるいはそれと気づかず、コネクタを破壊してまで逆挿ししてしまっているのです。その対応として、なるべく上下左右を分かりやすし、逆挿しできない構造をとります。
それでも、コネクタが小さくなるほど逆挿しによるトラブルは増えていました。そんな中登場したのが、Apple社のLightningやUSB-Cです。これは、システムやルールの改善としてとられる手法③「間違えそのものをあり得ないものにする(間違えても大丈夫にする)」の発想で生まれたコネクタですね。天地逆に挿しても全く同じように機能します。ユーザビリティからすれば、素晴らしい方法です。しかし、ギミックが必要で相応のコストもかかりますので、適材適所で適用する手法ですね。
尚、当社の基板対基板コネクタは、カスタム品等で特別なご要求がない場合は、敢えて極性をもたさず180°回転しても嵌合可能にしています。基板対基板コネクタの場合は、基本的に基板同士で位置や方向を判断するもので、コネクタとしては極性がない方が実装エラー等のトラブルが少ないだろうという考えの元です。このように、コネクタのタイプや使われ方によっても対応の仕方が変わってきます。それでは次に環境依存による接続不良に話を移しましょう。
コネクタは、本当にさまざまなものに使われます。そのため、コネクタを使っていただいている製品の置かれる環境や、その機能・機構によって機械的な動きが引き起こされることがあります。あるいは、意図せずもしくは意図的に叩かれたり投げられたりと・・・乱暴に扱われることもありますね。そういったときに、コネクタも機械的な影響を受けています。
あまりにこの機械的影響が強いと、見た目も分かりやすく、その製品ごと破壊されてしまうようなこともあり、各製品はその対策もとっていますが、そこに至る前にコネクタが戦う相手として瞬断という現象があります。瞬断という言葉はさまざまな局面で使われていて、たとえば一瞬の停電=瞬停等が挙げられます。しかし、今回説明するコネクタが戦っている瞬断はずっと短い時間で、μsec=100万分の1秒とか人が知覚できないようなレベルでの電気的不通なのです。振動や衝撃等の影響がコネクタに伝わった時、ほんの一瞬でも端子同士が離れてしまうとそれは起こります。
対策としては、「多少のことがあっても、ガッチリ接触させるバネ」設計ということになります。また、「コネクタとは」や、コラム別記事の「高耐熱コネクタってなんだろう?」でも触れていますが、高温環境下等ではバネ力が弱っていきますので、そこも配慮した設計が必要になります。
また開発されたコネクタが適切な耐震・耐衝撃性能を有しているのかを確認するために、試験を行います。実際に所定の条件の振動や衝撃を与え、オシロスコープ・データロガー(昔はペンレコですね)等を使用して、連続して健全な接続が維持できているかを確認する試験です。また、複合要因での耐久も加味するため、高温高湿下でそれを実施するバイブロチャンバーという試験機もあります。
試験設備に関しては、当サイトの信頼性の追求もご参照ください。これらの試験条件は規格で定められたものや、お客様の実際の実用から指定された条件等、さまざまなものに対応しています。厳しい機械環境で使われる製品に使用するコネクタの選定や評価等にお困りごと等がある方は是非お問い合わせください。
ところで振動に関しては、瞬断以外にもう1つ大きな戦う相手がおり、おそらく基板対基板コネクタにおいては、当社がコネクタメーカで初めて攻略したと自負しています。次にその話をしましょう。
振動環境下に物が置かれると、その物自体も振動を起こします。その振動の仕方は、その物の形状や質量に応じて定まる固有振動数に大きく影響され、共振という現象を起こします。
ここで、「置かれた物」の中で使われるコネクタに目を移し、基板と基板をつなぐ基板対基板コネクタについて考えてみましょう。コネクタがつなぐ上下の基板はそれぞれ異なった共振特性を持ちます。周辺から与えられた振動によっては、各々が違う周波数に反応したり、位相が違ったりと異なった共振を起こし、コネクタの端子にその振動の影響が伝わって接点が上下に動いてしまうことがあります。この上下の動き=ズレ自体は極めて小さなものですが、これが継続していくとフレッティングコロージョンという現象が発生し、電気接続を阻害します。
対策としては、まずは想定される振動に対して製品が共振を起こさない設計ができればよいのですが、継続的な振動にさらされる、たとえば自動車のパワートレイン周りの部品等はなかなか厳しい様です。そういった中で、当社では接点が振動による動きに追従するZ-Move構造をもつ製品を開発しています。
Z-Move構造では、接点が上下の動きに追従しますのでフレッティングコロージョンの発生を抑えることができます。基板の共振は、フローティングコネクタでは振動による連続運動によって可動片のバネの金属疲労による破壊も懸念されますが、当社のZ-Move構造を採用した製品は1億回の振動にも耐えうるように設計されています。
尚、Z-Move構造とはいえ、どんな振幅の振動にでも耐えうるわけではありません。そこで当社では電気接続に特化した独自の振動解析サポートも実施しており、適切な製品選択と併せてお客様の基板レイアウトに対するご提案も行っていますので是非ご活用いただければと思います。
では、その他の機械的な影響による接続不良について、見ていきましょう。
足で引っかけるというのは極端にしても(それに耐えた方が良いか否かは少しだけ後述します)、配策作業時のちょっとした力や物の移動で少し応力がかかった位で抜けてしまう例もあります。そういったアクシデント下でも電気を接続するため、コネクタはある程度の嵌合の保持力をもつ必要があります。端子の接続の強度そのものを上げても良いのですが、それでは今度は挿入しづらくなってしまうので、コネクタではロック機構をもつ製品が生み出されています。
図のようなラッチ機構のロックもあれば、ねじ止めタイプや、本体がねじ込むタイプのものを目にしたことがあるのではないでしょうか? そして各々の用途や、想定されるアクシデントに対して「XXN以上の引張耐力を保持すること」と規定され規格になっているものが多数あります。中間作業を考慮してロックをしている場合の保持力、ロックがない場合の保持力、双方の最低値が規定される例も多くありますね。
ここで規格によっては、最低保持力だけではなく「XXN以上の引張では抜けるように」と最大保持力が規定されていることもあります。すなわちコネクタ保持強度:Min. XXN & Max. YYN といった規定になるケースです。「強ければいいんじゃないの?」と思われる方もいるかも知れませんが、コネクタはあくまでも最終製品の一部として機能する機構部品ですので独りよがりに「自分さえよければいい!」という態度ではいけないのです。
どういうことかというと、次の図のような状況を想定しているのです。
コネクタの嵌合保持も重要ですが、さらに大事なものがあるということですね。図のようなもの以外でも、例えば図11で足を引っかけた人のことを考えた場合、その人が転んで怪我をしてしまうことを避けるためには、ある程度以上の力では抜けた方が良いという考え方もできます。安全はすべてに優先しますから。個人的な感じ方かもしれませんが、かつて壊れないようにひたすら頑丈に作られていた車のボディが、衝突の衝撃を吸収するために、ある程度、ある範囲でつぶれるような設計思想に変わっていったことと少し近い感覚をもちます。
あらためて、上の例をもう少し考えてみます。ケーブルが引っ張られたときに、ついにはその力に耐えられず抜ける、壊れるのは次の図の一番弱いところになりますね。
耐えるべき力ということでは、一番弱いところがそれに耐えなければいけませんので、各々強度保持のための設計がなされます。しかし、それでもどこかで限界は来ます。そうすると、次は抜けてしまう、壊れてしまうならば、どこでそれが起こるのが一番リスクが低いかと考えます。電線が抜けたり、ちぎれたりしてしまうと、感電や機器のショートといったトラブルにつながることもあります。基板からコネクタが外れたり、基盤そのものが破壊してしまったりと修理が大変そうです。そのため、ほとんどのケースでコネクタの嵌合が外れることが一番リスクが低いということになるのではないでしょうか。よってコネクタは、各々が頑張った結果一番弱くなった耐力の一歩手前で抜けてくれるのがベストのようです。そのためく「XXN以上の引張では抜けるように」という規定がされるケースがあるのです。機械的アクシデントの冒頭で出した例の「ケーブルを足で引っ掛けてコネクタが抜ける」にしても、あまりにポロポロ抜けても困りますが、それで転んで怪我をしたらその方が深刻ですよね(ただし、そもそもが人が足が踏み入れる部分にケーブルを這わせておかないことの方が重要ではありますね)。
ここまでWtoBコネクタを中心に説明してきましたが、基本的な考え方は他のコネクタでも一緒です(もちろん被る応力に違いはありますが)。そして、引っ張られる以外にも乱暴な扱いや、何か物がぶつかるといった機械的なアクシデントはさまざま想定されます。そう言ったケースに対しては、使われるアプリケーションと部位からリスクを推定し見合った程度に頑丈に設計していく対応をとります。やたら頑丈に作ると、大きかったり高価になったりしてしまうので、そこもまたバランスですね。またこじったり捻じったり・・・さまざまな意地悪試験も実施し検証しますし、規格化されているものも多数あります。加えて、お客様からのさまざまなフィードバックも貴重な情報になります。
また頑丈にという以外でも、たとえば誘い込み構造等も、アクシデントと戦う1つの対策ですね。先の「コネクタでの人為的ミスによる接続不良と対策」の内容とも類似するものですが、無理挿しをいなして正しい位置へ誘導するこの構造も機械的なアクシデントと戦う1つの機構になります。
誘い込みは平たく言えば、位置ずれして突入してきたコネクタをハウジングに施されたテーパによって正しい位置に誘導する構造です。このちょっとした構造でも、さまざまな工夫が施されます。例えば0.4mmピッチの10126S等では、コネクタが小さいこともありますので予備テーパを設けることで、誘い込みの効果をより高くしています(相手側は10126Bです)。
錫めっきから発生するウィスカと呼ばれる髭状のもの、銀めっきで発生するイオンマイグレーション等がこれにあたります。錫のウィスカは応力で発生し高温多湿化で成長が加速されます。銀のイオンマイグレーションは正極から負極へ電子を拾うために手を伸ばすようにしていく現象で、通電中の特に高温多湿化で発生し、リン酸等によって助長されます。40代以上の方は記憶にあるかも知れませんが、半導体の封止材に含まれた赤燐の影響による銀マイグレーション起因の接続不良でHDDの大規模リコールが起こったこともあります(コネクタではありません)。このあたりの話はコラム内の別記事「コネクタの端子にめっきをするのはなぜか?」でもう少し詳しく説明していますので、そちらをご参照いただければ嬉しいです。
完璧な対策というと、なかなか難しいのが現状です。たとえば錫のウィスカは、プロセスやちょっとした材質の選定等である程度抑えることはできます。ハウジングの構造等でブロックすることもできます。それでもゼロにはなりませんので、使用環境やコネクタの端子間隔(ピッチ)等から適材適所な使い方をしていくのが、最善の策になります。つまり、自分の得意な戦場に特化して、厳しいところは金めっきにお任せし、負けが決まった戦はしないといったところでしょうか。
異種金属間接触で発生する異種金属接触腐食(ガルバニック腐食)と呼ばれるものもあります。これは主に金めっきのピンホールがある場合等に問題があり、塩水噴霧試験で試験します。
対策としては、封孔処理等の手法がとられます。また周辺ガスによる腐食等が懸念されるケースでも、金属、特に材質と厚さ等が重要で、いくつかの種類のガス(SO2,H2S,NO2,Cl等がポピュラー)およびその混合体に対する耐性は所定の試験で検証されます。こちらの試験機も当社で保有しており、当サイトの「信頼性の追求」に掲載しております。これらについても「コネクタの端子にめっきをするのはなぜか?」でもう少し詳しく説明しています。
他、少し変わったところでは、低分子シロキサンによる接点接続不良という問題もあります。実はコネクタでこれが問題になったという話は聞いたことがないのですが(後で話題にでてくるワイピング機構のおかげでしょうね)、コネクタの親戚のような存在であるスイッチ系では時折起こる問題です。低分子シロキサンの問題はアウトガスの問題であり、厳しい用途ではさまざまな検証が必要です。幸い当社が良く使用するLCPやPBT等はほとんどアウトガスが問題になることがないエンプラです。それでも用途によっては、非常に厳しいレベルでのアウトガスや異物(機能妨害物)の発生の検証が必要なケースがありますので、都度さまざまな対応が必要となります。それではその流れで、次にはこうした異物をコネクタが受ける際の話に移っていきます。
コネクタは接続環境や接続までに接するさまざまな異物とも戦います。基本的には次のいずれかの対策で戦います。
・ 侵入させない
・ 侵入されても妨害されない
侵入されないに関しては後程ふれますが、わかりやすい例でいうとコネクタに付けるキャップがあります。
さて、それでは侵入されてしまった場合についてです。異物にはさまざまな物があります。粉塵、汚れ、金属、水・・・・まずは接触を阻害する側の絶縁物について説明します。侵入された(あるいはさせられた)場合の試験として、特に粉塵に関しては耐塵試験と呼ばれる試験があり、粉塵を充填させた中に一定時間コネクタをさらして後に取り出し所定の性能を満たしているかの確認をします。粉塵の種類はいくつかあり、指定されます。
絶縁系、接続を阻害する異物は粉塵以外にもありますが、コネクタがそれらと戦う機構はワイピングです。コネクタの端子同士は相応の接圧で押し付け合い接触しながら、有効嵌合長と呼ばれる距離をゴリゴリこすりながら嵌合していきます。ものによりますが、当社の代表的なコネクタですと、コンマ数mm程度のものが多いので感覚として捉えにくいかもしれませんが、ミクロの世界ではゴリゴリこすっているのです。この時にワイピング=ふき取りが行われます。
ワイピングによる異物との戦いは、「接圧=強さ」と「有効嵌合長=戦闘時間」をいかに異物と戦えるように設計すること、また効率よくワイピングを実行するための端子形状にすることがカギとなります。一方で、サイズの制約もありますし、抜き挿しに必要な力もいたずらに上げられませんので、全戦全勝の設計という訳にはなかなかいかないのです。
そこで二刀流的に武器を強化した、2点接点構造という技術があります。これは、前後に一直線に並んだ2つの端子によって構成され、前段の端子が異物を掻き出し、万が一これが異物に乗り上げてしまっても後段の端子で確実に接続するというものです。
実際に異物対応でお困りだったお客様が、この構造をもったコネクタを採用したことで状況が大きく改善したといううれしいフィードバックも度々いただいています。それ以降のお引き合いで2点接点構造をマストとされるお客様もいらっしゃいます。2点接点構造に関しては「コネクタの信頼性を向上させるオプション」でも、もう少し詳しく説明していますので興味のある方はご参照ください。
ショートにつながる異物といえば、水等の導電性の液体、金属粉および吸湿した埃があります。また結露が起こればショートにつながるリスクもあります。これらの問題は、吸湿環境ではただワイピングして拭い去ればいいというものではありません。入りにくい、あるいは異物が電極間をまたがらないような構造をとる必要があります。
IEC 60664-1(低圧電源系統内機器の絶縁協調)では、規定された使用環境の汚染度/汚損度で1~4までランク分けされた環境に対して、電気機器の構造と定格電圧が決められています。大まかな各ランクの環境は、次のとおりです。
汚損度1:クリーンな環境や密閉機器内
汚損度2:最も一般的な環境
汚損度3:工場内等の厳しい環境
汚損度4:主に風雨にさらされるような屋外
IEC60664で規定されている構造とは、周辺材質および沿面距離と呼ばれるものです。空間距離と沿面距離の違いは、次の図のイメージです。
どちらかといえば安全に関する規格のため定格電圧とセットになっていますが、基本的な考え方は「導通するものが電極間で届かない(届きにくい)」状態とするものですね。この考え方は、さまざまな導電性異物への対策とも共通します。実際にコネクタに施される構造的な対策はより複雑ですが、シンプルな対応と環境の程度によっての限界をイラストにしてみました。
結露や金属製の異物によってショート接続不良が懸念される場合、むき出しになっている金属部にそれらが届かないようにしてやればいいということになります。シンプルに間隔=距離を大きくとったり、防護壁のような構造を踏襲したりすることで、ある程度までの異物に対しては効果をもちます。しかし想定を超えた大きさや量の異物が侵入してしまうと、またトラブルが発生します。ここでどのような場合でも耐えうるようなコネクタを造ろうと思うと、ただただヘビーデューティなものになって可用性が損なわれてしまうケースが多発します。もちろんヘビーデューティなコネクタも実際に需要があるのですが、全部が全部そういったものにしてしまうのはコスト面でもサイズ面でも現実的ではないのですね。
そういう意味では先に上げた想定が非常に大事なのです。各コネクタメーカはこの課題に限らず、製品開発時にはさまざまな製品仕様は「この製品をどういった市場、どのようなアプリケーションで使っていただくか?」を入念に検証し製品仕様を決め、詳細構造を決定していきます。コネクタを使用されるお客様においては、コネクタメーカの営業員から度々用途を聞かれたり仕様書にある免責項目を目にしたりされた方も多いかと思いますが、それにはこういった背景も含まれているんですね。さて、その想定に対して、あるいは取り入れた対策に対して、効果の検証はもちろん、評価も実施します。たとえば結露等は各種条件の温湿度のサイクル試験での検証を行っています。度々登場する当社の信頼性実験室でも該当設備を有していて、日々さまざまな製品での評価を行っています。
最後に、異物の侵入に対する規格に関してお話をします。
製品に対する異物の侵入を規定するものとしてはIECのIP規格が有名で、耳にしたことがある方も多いのではないかと思います。IP=International ProtectionでIPXXと2桁の数字でグレード分けされます。防水規格のイメージが強いのではないかと思いますが、XXの前段は人体および固形物体に対する保護で0~6の7段階に分かれます。グレードはざっくりで言えば、侵入できる(侵入を防げる)物の大きさで決まっていて、小さくなるほど高グレードです。最高グレードの6では、完全防塵になります。XXの後段がおなじみ防水のグレードです。0~8の9段階だったものが、最近ドイツ規格でジェットスチーム洗浄に対する9Kが加えられ10段階で認知されています。実際に適用されるグレードを一覧化しました。
マトリクスでグレードが存在しない箇所がありますが、 たとえば指は危ないところに届くけれど水は侵入しない、ということはないのでIP18はないのです。どういう状況を想定しているのかが非常に判りやすい規格です。この規格はコネクタのような部品に対してではなく製品についての規格であり、機器の中で使われる製品が主体である当社の製品ではあまり直接的に引用することはありませんが、「車載同軸カメラソリューション」で紹介している同軸(FAKRA)インターフェース付きカメラリアケースは、IP69Kに対応した製品となっています。
接続不良の要因と対策ということで、説明してきました。接続不要の要因と対策は、次のようにまとめることができます。
(1)不完全嵌合
対策:クリック感とAudible Click(可聴クリック)
(2)誤嵌合
対策:コネクタの色分け、Key Feature、逆挿しできない構造
振動・衝撃による瞬断
対策:バネ
振動による微摺動摩耗
対策:Z-Move構造
機械的なアクシデント
対策:ロック機構、誘い込み構造
(2)化学変化による接続不良
金属からの成長物 ウィスカ、イオンマイグレーション
対策:適材適所での使用
ガルバニック腐食(異種金属接触腐食)
対策:封孔処理
(3)異物による接続不良
粉塵
対策:ワイピングと2点接点構造
導電性の液体、金属粉および吸湿した埃等によるショート
対策:IEC 60664-1
今回のコラムをきっかけに、「金属同士が触っていれば導通する」から「コネクタも大変なんだなぁ」という感じ方に変わったという方が少しでもいらっしゃれば、当社あるいはこの業界で頑張っている面々も少しは報われるのではないかと思います。そして、コネクタに限った話ではなく、さまざまな電子製品、電子部品は、普段意識しないような細かな所まで工夫や検証を積み重ねているのです。私もついつい忘れがちになりますが、コネクタ以外にもさまざまな製品に施された細かなテクノロジーやそれを支えている方々への感謝を再認識いたしました。